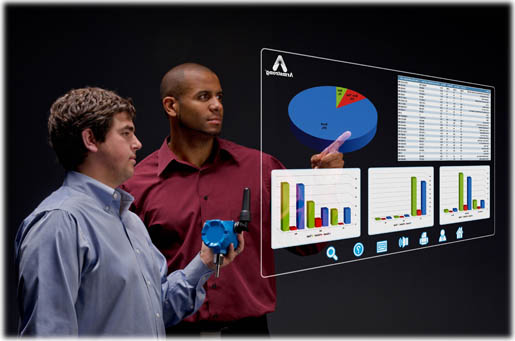
FINALLY, THE MEANS TO ACHIEVE BEST PRACTICE STEAM SYSTEM MANAGEMENT
Energy costs continue to fluctuate. Increasing right along with them is the awareness—greater than ever before—of how important steam trap maintenance is to conserving energy and saving dollars. But awareness is one thing, action is another. Energy users at every level are still faced with problems that are products of outdated thinking and misplaced priorities:
- CONTINUAL REDIRECTING OF LABOR, LEADING TO START-STOP MAINTENANCE PROGRAMS
- LOST PRODUCT BECAUSE OF UNEVEN PERFORMANCE
- INACCURATE AND INCOMPLETE REPORTING
- INABILITY TO STANDARDIZE ACROSS MULTIPLE FACILITIES
- TESTING AND RESPONSE THAT ARE ALWAYS TRYING TO CATCH UP WITH REALITY
THREE CHALLENGES – ONE INTELLIGENT SYSTEM SOLUTION
Three constant challenges that plant managers and maintenance personnel face in the operation of any system include:
Identifying a failure: ability to immediately pinpoint what has failed, when it failed and where it failed.
Evaluating the scope: comprehending the magnitude of the failure related to process and utility systems.
Measuring the impact: accurately calculate the costs including process disruptions, wasted energy and plant shut downs, safety hazards and fines levied.
AIM® enables your team to tackle all three challenges with one system solution that combines a mix of methods including acoustic and temperature monitoring with integrated smart wireless solutions that deliver:
- IMMEDIATE FAILURE NOTIFICATION OF DEVICES SUCH AS STEAM TRAPS
- IMMEDIATE NOTIFICATION OF RELEASE TO FLARE FOR EMISSIONS MITIGATION
- PINPOINT ACCURACY OF FAILURE LOCATION FOR FAST RESOURCE DEPLOYMENT
- DETECTION OF “SIZZLING” RELIEF VALVES FOR PROACTIVE MAINTENANCE SCHEDULING
- PREEMPTIVE WARNING OF HAZARDOUS VAPOR RELEASE TO IMPROVE WORKER SAFETY